Soldering is a useful skill that can help you achieve efficient results whether you want to use it for DIY projects or business purposes. Soldering is not only for a handyman, but it is also for people who need to do a simple fix or assembly of electronics. Generally, it is primarily used to join two workpieces by melting a solder. It is suitable for installation, repairs, and crafts, making it one of the most used processes in the industry nowadays.
It is crucial to understand the basics and proper methods to apply. It will allow you to ensure that you are getting your desired results. Before you choose the right kind of soldering iron for your project, make sure that you understand the difference between a butane-fueled and electric-powered tool to make shopping easy and convenient for you. So, start by checking out the uses of a soldering iron, types of materials that you have to prepare, and the most important is, knowing the safety tips that you need to implement during the process.
- Uses of Soldering Iron
- Primary Materials for Soldering
- Fume Extraction Equipment
- Additional Things to Consider
- Importance of Heat Temperature
- Using the Fuel Tank
- Using the Open Flame
- Things to Remember Before You Start Soldering
- Soldering Process
- Things to Do When Soldering Fails
- Soldering Safety Tips
- Additional information
Uses of Soldering Iron
Many industries depend on the technique of soldering iron. It is primarily used to join spare parts of an object. It involves different stages, and one of the essential steps is melting the metal parts so that it will be easy to connect them, or also called solder. The solder looks like a metallic glue, and when it hardens, it can strongly join the components.
Recommended: Top 5 Butane Soldering Irons
Soldering is a technique that can be utilized in different ways. It is suitable for arts and crafts projects like home decorations. It is also helpful in plumbing to connect or repair broken pipes. Furthermore, it is an essential method to join engine components neatly and efficiently. The makers of jewelry also use it primarily to solder small components of these objects.
People who love artwork may also take advantage of soldering iron. You can find the pyrography professionals using it to put burn marks as a way to uniquely decorate wood. It can even be used for plastic welding and major installations.
Generally, soldering should meet the right heat temperature which is around 400 degrees Fahrenheit. However, it should accede this standard when it is used for welding purposes. One thing that makes soldering iron stand out in many industrial applications is that the metals being connected do not easily melt although they are placed in lower temperatures. They do not quickly warp, and instead, they stay on their shape despite being used for an extended period.
If you want to use soldering in your DIY project, you don’t have to acquire a specific skill for you to learn how it works. Whether you need it for connecting truncated jewelry or broken pipe, you can rely on it to produce efficient results.

Primary Materials for Soldering
As mentioned, soldering can be done in easy steps. However, the choice of solder needs to be considered when you want to come up with excellent results. Take note that there are various kinds of solder available in the market. The outcome of your project relies on the different standards that you use during the soldering process. So, regardless of the project or your purpose, check out the following materials used generally in soldering procedures.
Soldering Iron
The soldering iron is one of the first essential things to consider. Take note that it is the primary material of the process, serving as the source of heat. It is used to melt the solder which is also another crucial method. Irons also have different ranges, and it determines the application wherein it is suitable. Those between 15W to the 30W range are appropriate for the electronics industry and printed circuit board projects. Those that exceed this standard may damage the components of electronics. If you want to solder a thick wire and heavier components that require more durable results, then you must use an iron with a higher range which is about 40W or more.
The soldering iron is the primary tool that the hobbyists in the electronics field need. It is suitable for assembling small components in the printed circuit board because this material has a tiny tip. It also prevents the risk of damaging the circuit board due to its low heat capacity. With the help of the soldering gun, you may use it in heavy duty soldering processes. Some of its useful applications for the latter usage are joining brackets into the chassis and connecting large gauge wires.
The soldering iron must also have a three-pronged grounding plug. The purpose of this material is to control the voltage that might collect the tip of the solder. This step prevents the occurrence of any accident which may not only damage the components but the user as well. If you are a beginner, it is advisable to use an iron ranging from 15W to 30W. However, you have to make sure that as you get used to your skill, the standard should also increase.
Being said, you might find it hard to connect the larger components when you use 15W. So, as your capability improves, you can level up to 40W iron because it is capable of joining heavy materials easily. This standard is suitable for more powerful irons because it will help you save your time when heating it, which can result in breaking the components.
Solder
Take note that there are different kinds of solders, and not all types are suitable for electronics use. You have to make sure that you will not choose an acid core solder for this purpose because it contains an acid, a chemical that can damage the printed circuit board. Furthermore, it is also responsible for destroying the component leads. This material is primarily used for soldering copper.
In terms of size, it is recommended to use a solder with a diameter not less than 0.75MM and not greater than 1.0MM for a printed circuit board. The board has small joints that you need to connect it is why it is better to select a smaller solder. On the other hand, you may use a thicker solder when you need to connect larger joints without spending too much time on the heating process.
Thicker solders are not advisable to be used on circuit board work to prevent the forming of bridges between the spaces of PCB pads. Commonly, electronics experts use an alloy of 60/40 for their work. It means that the solder contains 60% tin and 40% lead. You may also choose those that do not contain a lead.
Soldering iron stand
For your extra safety, you may also use a soldering iron, which is a safe place to store the iron when not in use. It can also be a sturdy storage where you can keep the cleaning supplies.
Safety glasses
It is also essential to use safety glasses to protect your eyes aside from keeping it away from the fumes. These fumes are hot which can cause a burn. There is a big possibility that they spit in different directions while you are trying to heat the metal. Aside from its danger in your skin, your eyes are not also exempted from the irritation.
Soldering station
A soldering station also plays a critical role during the soldering process. It has the specific control in adjusting the settings and essentially, the temperature of the iron. This place is where you plug in the iron.
Also: Our Favorite Soldering Stations
Cleaning Pad
Keeping the iron in its excellent performance is crucial for you to come up with efficient results. It is why investing for a cleaning pad so that you can keep it clean and avoid rust.

Fume Extraction Equipment
Normally, the soldering area is filled with hazardous gases once the process takes place. It is why having fume extraction equipment is critical. It acts by purifying air to filter out the poisonous smoke from the working place. It keeps you safe while the process is ongoing and minimizes its impact on your respiratory system. Therefore, aside from the making sure that the place is well-ventilated, you should also make sure that you have the fume extraction tool ready.
This list includes important materials that are usually used in soldering methods. Aside from these tools, keep in mind that soldering iron also has different types. However, two of them stand out when it comes to a wide variety of usage, benefits, and efficiency. If you are torn in choosing between butane soldering iron and electric soldering iron, you’ve come in the right page. Go over the difference between the two and know which of them suits your needs.
Additional Things to Consider
You must make sure that you are using the right kinds of equipment before starting your work. Since there is a wide variety of soldering irons and solders available in the market, you have to consider the following guidelines when choosing the tools and materials needed for your project to ensure that you are in the right track.
Take note that it is required for you to use a 25W to 40W soldering iron if you need to work on electronic circuits. However, if you need to solder larger components, soldering irons with higher wattage are essential for the project. So, make sure to consider the watt capacity of the soldering iron when you are shopping for this tool.
Remember that the solder possesses a lower melting point compared to the components that are being connected. Consider the rosin core as well because it plays a significant role in the outcome of your project. It acts as a flux and is a helpful material that controls oxidation of the metals involved in your project. It also contributes to how the solder wets the components that are being connected.
If you need to join copper pipes, then the solder must contain an acid core to make it suitable for this purpose. However, this type of solder should not be used for electronic connections because it can cause corrosion on the components. It is, therefore, essential to choose a rosin core.
For electronic purposes, a solder must have a diameter between 0.75 millimeters to 1.0 millimeters. Exceeding these standards might cause solder bridges on the areas where the components should be connected, resulting in the unrefined finish.
An alloy is also suitable for many electronics projects. 60% of its content is tin while 40% is lead. You may also use a lead-free solder if you prefer. You may also use a stand for your safety and convenience. It is used to hold the soldering iron when it is hot.
Check Out: Repair Your Guitar with these Soldering Irons
You also need to prepare a solder braid, a tool which is used to remove the solder. You only need to place it on top of the solder while heating it above with the iron. As the heat increases, the solder will automatically flow with the solder braid. It is also a helpful material when removing the electronic component that is already attached to the board. Furthermore, it can also reduce excess solder on the connection.
You might also need a prototype board when you are working for an electronic project. It is where you need to assemble the components. It includes copper tracks that are used to join the parts. Prepare your steel wool as well because it is essential to clean the connections before the soldering process. Keep in mind that the solder will not flow when the part is dirty. Using crocodile tips are also helpful when the heat sinks.
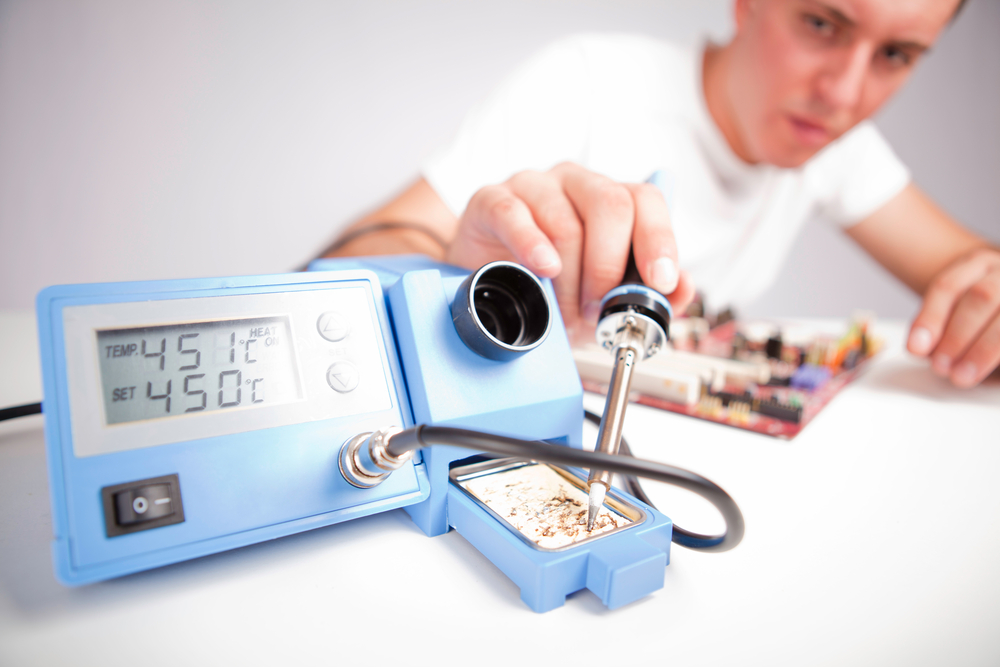
Importance of Heat Temperature
Solders have different melting, and flowing point temperatures and both play a significant role during the process. The outcome of your project also depends on this aspect. It is also recommended to use a higher temperature when you are working with multiple soldering on just a single piece. A low-temperature solder is not advisable when you are doing several soldering processes. The method also involves reheated zinc but can decompose when you use a lower temperature. It can also leave pits, which usually remain unsightly and can bring a negative effect on the outcome of your project.
The involvement of zinc also affects the melting temperature by lowering it. It is also possible that a yellowish-gray line will be left on the silver. It is one of the reasons why you must clean the solder ghosts or excess solder. Oxidizing the blobs with sulfur will not resolve the issue. Trying to cover it up can make it even more noticeable.
If you are trying to create pieces, then, you must use a hard solder. It is essential most especially when the piece collapses once heat is combusted. Using a high temperature may cause the already soldered joints to disconnect. Both medium and hard solders are also used for closing rings. This application needs the highest temperature to prevent oxidation, which is characterized as the yellowish-gray color that appears on the silver.
Different alloys have their appropriate melting temperature. Refer to the list below and find the exact temperature that you need to achieve when soldering the type of metal.
• Aluminum – 1220
• Bronze – 1825
• Copper – 1983
• Fine Silver – 1760
• Nickel – 2030
• Pewter – 440
• Platinum – 3223
• Red Brass – 1880
• Sterling – 1640
• 14K Yellow Gold – 1615
• 18K Yellow Gold – 1760
Remember the following melting or flowing points of solder you may use for your project.
• Easy solder
Melt – 1240; Flow – 1325
• Medium solder
Melt – 1275; Flow – 1360
• Hard solder
Melt – 1365; Flow – 1450
• Intense temperature
Melt – 1340; Flow – 1460
Using the Fuel Tank
The fuel tank is responsible for holding the butane gas. Therefore, you need to fill it with fuel to ensure that you can use it whenever needed. Start by holding the tank in a vertical position and making sure that it is switched off. It is to avoid any accident that may occur. It is also crucial to ensure that the equipment is far away from any naked flames.
Press down the standard butane gas firmly and wait for a few seconds until the tool is full. Usually, full tank soldering iron lasts for about 45 to 90 minutes operation, but may also vary according to how you are using it.

Using the Open Flame
In some arts and crafts projects, the use of open flame plays a significant factor in the design of the object. It is why most soldering irons nowadays are also equipped with flaming features or torch. To make use of it, you have to remove the catalyst which is located on the end of the solder. Loosen the flame guard by unscrewing it until the catalyst appears. Then, ignite it by putting back the flame guard and positioning your thumb on the child lock to push it forward. Lastly, pull the trigger, release it quickly and you will see the flame coming out from the solder.
Related: Top Recommended Gas Soldering Irons
Thankfully, it is also possible to control the amount of flame that comes out from the solder. You may also set it to work continuously if the project requires it.
Turn the flame on by doing the earlier method. Then, keep the lock switch on by pressing it. Now, if you want to control the size of the flame that comes out from the tool, wait for it to cool if you previously used it. Remove the flame guard and attach the catalyst. Lastly, put in the flame guard again and tighten. Then, turn it on.
If you want to produce a medium-sized flame, then you have to set the torch to this standard. Ignite it and wait for a few seconds until it is heated. Then, touch the solder to the tip of the component until it melts.
These methods of setting the soldering iron into different flame sizes also have specific rules for safety and efficiency. Avoid using the electrical tin solder since the solder supplied is mainly used for electrical works.
Since it is fueled with butane, it doesn’t require to be connected to electrical power. It is also best to use for connecting small components. Make sure that you clean the soldering iron once you are done. Do it by wetting the sponge or cleaning pad included in the kit. Then, wipe it over the tool until it is thoroughly cleaned.
The sizes of the flame depend on the project that you are working on. If you want to achieve a fine detail, then you have to adjust the flame into a smaller size. For those who need to solder jewelry, then, they must switch to a medium flame.
Now that you know the advantages of using a butane soldering iron for whatever project you are trying to work on, it’s time for you to see the benefits that an electric soldering iron also has.

Things to Remember Before You Start Soldering
As part of your preparation, there are also key guidelines that you need to keep in mind to keep you safe during the process. Knowing the precautions are as crucial as preparing the materials needed.
A soldering iron powered by an electric can heat to 400 degrees Celsius. Due to this reason, an accident may cause a fire which can be damaging to the entire property. It is, therefore, crucial to unplug the tool when it is not in use.
You also need to make sure is to avoid putting the power cord on places where it might trip over. Do not touch the tip of the soldering iron when it is connected to the electrical line because it can lead to electric shock. Do not even place it on the workbench because it can also result in an accident.
Ensure that your workplace is well-lit and properly ventilated because the process usually emits smoke while melting the solder. It will irritate your eyes and respiratory system, preventing you from breathing properly. The solder material may also contain lead, a poisonous metal that can lead to suffocation and other health issues. It is also crucial to wash your hands once you are done with soldering.
Since you are using an electric-powered soldering iron, you have to make sure that your working area has a reliable electrical connection and there is also an excellent flow of circuit. Before you start the work, make sure that you have all the materials completed to avoid hassle and inconvenience during the process.

Soldering Process
Soldering requires a step-by-step process to ensure that you come up with efficient results. Make sure the surface is clean so that you’ll achieve a fine finish. Use steel wool to polish the copper coil on the PC board before getting started. Ensure that space is free of wax, paint, or oil.
To get started, keep the tip of the soldering iron heated for a few seconds. To do so, put it in the stand. Then, plug it in and wait until it fully heats up. Once you are sure that it is already hot enough, hold the soldering iron just like you are holding a pen, but position your hands near the lower part of the tool handle. Ensure that both components are hot enough to create a fine connection.
Then, melt the solder using the tip of the iron, a process called tinning. It is one of the most crucial methods of soldering because it can provide an excellent flow of heat from the tip of the iron to the joint. It is essential that the solder continuously flows to the tip to produce a shiny surface. If it does not happen, you have to clean it using a wet sponge.
You Might Like: RC-Suited Soldering Irons for Hobbyists
Tinning doesn’t have to apply at every point. However, this process is helpful when the tip becomes dull after a few minutes of not using the soldering iron. Once tinned, you should remove excess solder to ensure that you achieve the best results. You will know if you were able to make it perfect when the tip of the soldering iron looks shiny and silver. It is recommended to replace it when it looks blackish.
The tip of the soldering iron can connect the lead of the electrical component to the copper pad by heating them. As soon as the solder melts, it can easily join metals when they contact together. You only need enough solder to join the components to avoid creating bridges between the connections.
Make sure that you remove the tip of the soldering iron quickly once you have noticed that the solder is enough to create the connection. Wait for the connection to cool down before moving it. Take note that too much heat can damage it. You can use the crocodile clip to prevent it from happening. It can absorb the heat to control it from constantly sinking through the components, thus, preventing the damage it may cause.
You are making the right connection when it forms a triangular shape. You may reheat and melt it again if you see that the connection is bad. Ensure that the formation is solid and intact before finishing the procedure.
Don’t forget to clean the tip of the iron with a damp cloth and leave it shiny. While doing this final process, make sure that the soldering iron is also unplugged.
Things to Do When Soldering Fails
Soldering may sometimes fail most especially when it is your first time doing it. If you noticed that the solder wouldn’t flow, that means that the components that you are trying to connect are dirty. If this issue occurs, remove the solder and use a cleaning pad to remove the dirt.
If you see that the connection looks crystalline, it means that the parts were moved even before the solder cools down. However, there is still a way to improve its joint. Reheat it, or may also try to use a larger soldering iron to correct the issue. In that way, the solder will be able to get enough heat to eliminate the grainy parts.
Sometimes, the tip also looks oxidized. If it occurs, the simple and easy way to fix it is to clean the tip. In that way, you will be able to produce a shiny tip. It is best for the synthetic sponge and cleans it while the tool is still hot. You can also prevent this issue from happening by unplugging the soldering iron when you are not using it.
Make sure that you are only using the required amount of temperature which is only enough to melt the solder. You should clean the tip of the iron as soon as you noticed the silver color is starting to fade or becomes black.
As mentioned, using too much solder can produce bridges on the connections. It often happens when two joints were connected accidentally. It also means that you are not using the right amount of solder. It can also affect the process, thus, preventing the electrical circuit from going through the board and component. It is, therefore, critical to ensure that you meet the right amount and heat temperature to produce a smooth and shiny connection.

How to Remove Solder
The primary tool that you will be using in this method is the solder pump. It is commonly called a solder vacuum and sometimes, solder sucker for others. It is a handy suction tool that works like a vacuum. It can suck small amounts of solder by melting the joints. This device is also available in different kinds, and you may choose one that is powered by electric. For some, a manual type also works the best because it is featured with strong suction, allowing efficient and easy job in removing the melted solder.
1. Setup your solder pump.
2. Touch the tip of the preheated soldering iron and point it directly to the point that you want to disconnect. Keep the soldering iron steady while the solder is flowing.
3. Hold the soldering iron in place. Then, get your solder pump and move it closer to the melted solder.
4. Allow a small space between the solder pump and the melted solder. Press the release button and observe while the tool performs the suction. Wait until you see that the melted solder is completely removed.
5. Lastly, let the melted solder cool down inside the tool before pumping all the debris out.
You may also use a desoldering iron to remove the solder. Just heat this tool just like how you do in a standard soldering iron. As the vacuum runs, put the device closer to the joint that you want to disconnect. You will notice that the solder slowly liquifies. Then, the suction of the liquified solder starts.
Soldering Safety Tips
Although soldering is not an accident-prone activity, it is still crucial to remember a few tips to keep you safe during the process.
Keep in mind that this process needs high temperatures if you want to come up with efficient results. Soldering irons utilize 350 degrees Fahrenheit heat, which can lead to burn when you are not careful.
To avoid burn, make sure that you put the iron in a stand while keeping the cord away from it. Aside from avoiding its harmful effect on your body, you can also reduce the risk of the electrical circuit. Accidentally burning the cord can expose its hidden components that can lead to the fire.
Make sure that the working area is well-lit and there are no clutters to make it easy for you to move around. Ensure that there is a dedicated space for materials where you can lay them safely.
Remember that there might be some small components involved in the process, so make sure that kids and pets are restricted to go near this area.
Your life may be put at risk when you solder a live circuit. It is because the electricity travels through the wire going to the soldering iron. When it happens, it can surely hit your body. Therefore, the first and foremost thing that you have to make sure is to disconnect the circuit before you start to solder.
For projects that require connecting two wires, use tweezers or clamps with a rubber handle to hold them. Remember that wires conduct electricity which means that it can cause burn or injury when you try to hold them with your hands. It does not mean that soldering is safe to do when you feel that the wire is not hot. It can raise its temperature at any time, resulting in an accident.
The soldering process can also affect your respiratory system and eyes due to the fumes produced by the heated components. Therefore, make sure that you keep your face away from the joints that you need to connect to avoid irritation.
Avoid touching your face, eyes, and skin while doing the process. Wash your hands when you are done to remove the lead which is mostly found on most solders.
Also Read: Our Highest-Rated Soldering Irons
Whether you are working for electronic projects, repairing broken pieces, or creating arts and crafts, using a soldering iron is a reliable process that will help you along the way. You only need to determine the right kinds of a tool suitable for your purpose, and it will give you efficient outcomes. Whether the soldering iron is powered by electric or fueled with butane, you have to make sure that any of these two should be suitable for your project. With a lot of materials and equipment available in the market, soldering doesn’t need to be complicated as long as you know the exact steps on how to achieve your desired results.
Additional information
Now that you already know the steps and basic guidelines on using a soldering iron, it is time to gather the facts about this technique. The following summarizes the important things that you need to keep in mind whether you are an aspiring jewelry-maker, electronics technician, or you are only doing it for a hobby.
Copper Solder Paste for Solder vs. Silver Solder Paste for Silver
The copper solder paste, although called copper, does not look like copper. Instead, it is dark gray and may also appear as bright silver when applied to the copper metal. Silver solder paste, on the other hand, only turns bright silver to indicate that the solder has flowed.
Brass Turns to Copper in Color After the Soldering Process
This color normally appears due to the alloy mixes with brass while the piece is being fired. During the process, zinc was depleted by heat on the outer layer, while a portion remains. To correct this issue, create a mixture consisting of 2 parts hydrogen peroxide and 3 parts white vinegar. Then, soak the piece into the solution, and you will notice that the copper color slowly vanishes. Wait for about 30 to 60 minutes and the metal will become a yellow brass again. The color will not instantly appear. Instead, it will come out hazy as you take it out. Polish it to achieve your desired shine and smoothness.
Avoid soldering on a house brick because it can absorb the heat coming from the torch as well as the piece will never reach its required temperature.
Soldered Pieces Fall Apart when Placed in A Cooling Cup
If this issue occurs, it means that the heating temperature is not controlled properly. Some portion of the piece may melt when the heat goes in too fast. Although it was indicated that the entire piece should be heated, make sure that this process is happening slowly to ensure that the solder receives the right flow while the pieces are being heated uniformly. Also, you have to make sure that you are filling the gaps. By doing so, you are creating sturdy jewelry that can last longer.
Another tip is to clean not only the metal but the solder as well. Sometimes, dust and dirt covering either of these materials are the culprits. The tiniest particles and even grease transmitted from your hand can compromise the durability of your jewelry. So, keep them clean before using. Wash your hands properly and use a pair of tweezers to hold the metal and other tools.